G.R. ELETTRONICA, ELECTRONIC
BOARDS AND RELIABILITY (MTBF)
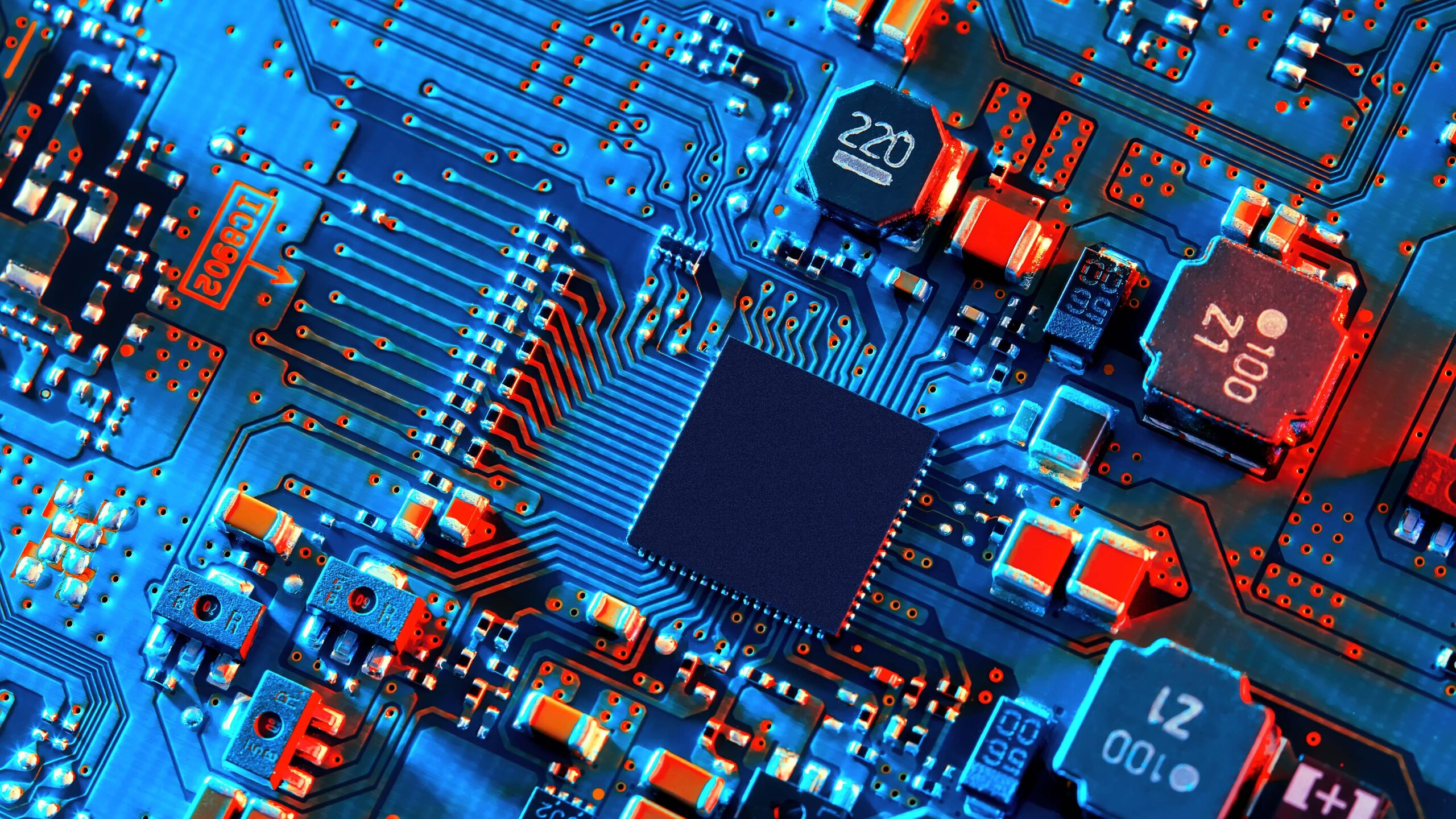
The reliability of electronic components and production processes play a priceless role in securing customer satisfaction, with a strong impact on the safety of products released on the market.
Calculating MTBF (Mean Time Between Failures) is one of the basics of sid reliability: it aims to predict the defectiveness of a device during its useful life. The MTBF can be determined by experimental tests or, in the case of electronic boards, also by specific standards. The value of MTBF is a fundamental requirement for the customer.
AtG.R. Elettronica, the continuous technological and productive improvement has allowed us to achieve very high levels of reliability for the electronic devices and systems of our production, greatly reducing their failure rate.
During the input stage, all components are checked and labelled to ensure traceability and correct assembly.
Production is carried out using automatic lines equipped with the latest generation of positioner machines, which offer a dynamism that allows us to perform extremely diverse kinds of production, from prototypes to series production.
The correct execution of the production process is also guaranteed thanks to the optical inspection performed either by an operator or through Automatic Visual Testing (AOI), carried out during the assembly, welding and end-of-working processes.
G.R. ELETTRONICA carries out a verification and/ or testing on 100% of the boards produced.
The correct functionality of the product is guaranteed, with Functional Testing of the boards and equipment realised, following the established procedures and using simulators as well as dedicated and automatic testing systems for the detection of electrical parameters and impedance.
For reliability predictions (MTBF) it is necessary not to limit oneself to theoretical calculations but to carry out specific stress tests, which aim to accelerate the failure mechanisms and verify the solidity of the product. These accelerated tests make use of factors such as temperature, humidity, current, voltage, and are often referred to as Burn-in.
At the request of the customer we can include these assessments in our production cycle to identify and cut out those products that have defects that will manifest themselves in time, that are not, therefore, usually detectable through the normal control tests in production.
This aspect is particularly important not only for guaranteeing the continuity of the service of the product, which in some sectors is vital, but for the ordinary and extraordinary maintenance of the products in which our electronic cards are inserted.